为打造行业智能制造新模式增强企业市场竞争力
推进工业化与信息化两化深度融合是当今各国先进制造业发展面临的共同课题,智能工厂是推动我国两化深度融合的重要着力点。某制造业企业以目前信息化、自动化的建设为基础,建设基于CPS的智能工厂项目,通过“建立二个平台、实现五个仿真、建立一套标准、推动二级创新”,为打造行业智能制造新模式、推进智能制造进程进行试点验证,进一步增强企业的市场竞争力。
解决方案
数据管理平台
通过数据管理平台,实时采集工厂数据并上传到物联网平台。将工厂碎片化、离散、孤立的数据信息进行汇聚、清洗、转化、沉淀转化为企业数据资产。提供一站式智能数据管理能力,帮助企业快速构建从数据接入,到数据分析的端到端智能数据系统,消除数据孤岛,统一数据标准,实现数字化转型。
微服务平台
通过建设有效微服务,为应用提供前端页面、后台数据及逻辑计算。包含新生产前实时仿真服务、新生产中实时仿真服务、新生产后回溯仿真服务、产品制造生命周期服务、设备运行生命周期服务、数字孪生服务等。采用微服务完善的工具链,逐层堆积组件集,按需构建应用。实现企业在信息系统开发、测试、运维过程中的平台统一、入口统一、技术架构统一、管理统一。
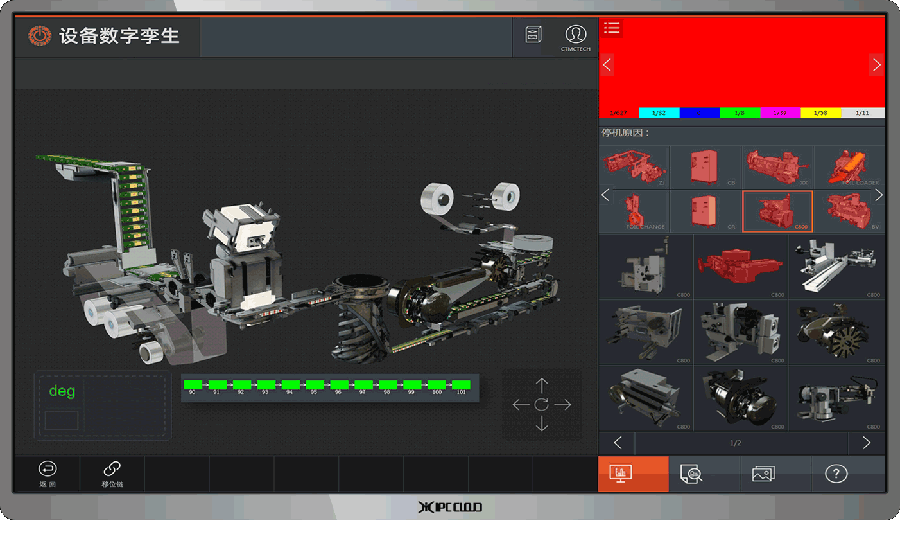
生命周期管理
产品制造生命周期仿真提供站点管理功能,提供自定义产品链路配置操作;基于“数据查询配置”,建立站与站之间的关联关系,实现任意站点的跳转追溯以及追溯过程中相关联的数据展示。设备运行生命周期仿真是基于设备图纸展示设备BOM信息,结合设备历史数据和实时数据,实现设备监视和报警,为设备生产过程分析、设备效率分析提供支撑。
价值赋能
数据采集
实时采集工厂数据上传到物联网平台,对生产过程中的状况实时监控,为生产决策提供有力的数据支持;将关键信息存储到数据库中,运用数据挖掘技术对各项指标进行统计分析,全方位反映生产过程。为工厂信息化建设打下基础,提高工厂信息化建设水平。
数字孪生
通过数字孪生系统对各机型进行3D建模,并以数据管理平台的实时数据和业务数据为基础,实现对车间生产现场的3D实时监视,为维修、运维提供可视化拆解视频支撑,为领导层提供远程监视页面,有效提高工作效率,降低学习成本。
生产前虚拟仿真
根据订单预演生产,对从原辅料的出入库到成品产出的制造全过程进行模拟仿真,优化人员、设备、物料、计划等资源的配置;构建一套完整的虚实映射生产数据模型,根据预演结果向各环节下达批次生产工单,组织实际生产,通过生产预演提升资源配置能力。
生产中实时仿真
生产中实时仿真建立工厂、车间、设备架构,建立工厂模型、生产线模型、设备模型、产品模型等,应用虚拟仿真技术将生产线的生产过程、设备运行状态、物料跟踪状态实时虚拟化,为企业管理搭建数字3D可视化管理平台,提升企业管理能力。
生产后回溯仿真
生产后回溯仿真基于数据归集、建立多条件组合式查询(时间、工厂、车间、机台、牌号、班次、班组)、根据不同业务需要进行组合查询,得到数据统计结果。为企业提供手段和方法来追溯产品在生产过程的质量控制情况,实现产品质量分析,提升生产过程的质量管理水平。
生命周期仿真
通过产品制造生命周期仿真服务,提供产品全过程数据分析服务,在生产过程中更好地指导各质量监控点,提升企业生产质量的把控能力。设备运行生命周期仿真服务支持对边缘层生产设备、检测设备的有效监视,结合设备历史数据和实时数据,实现设备监视和报警,为设备生产过程分析、设备效率分析提供支撑。
成功案例
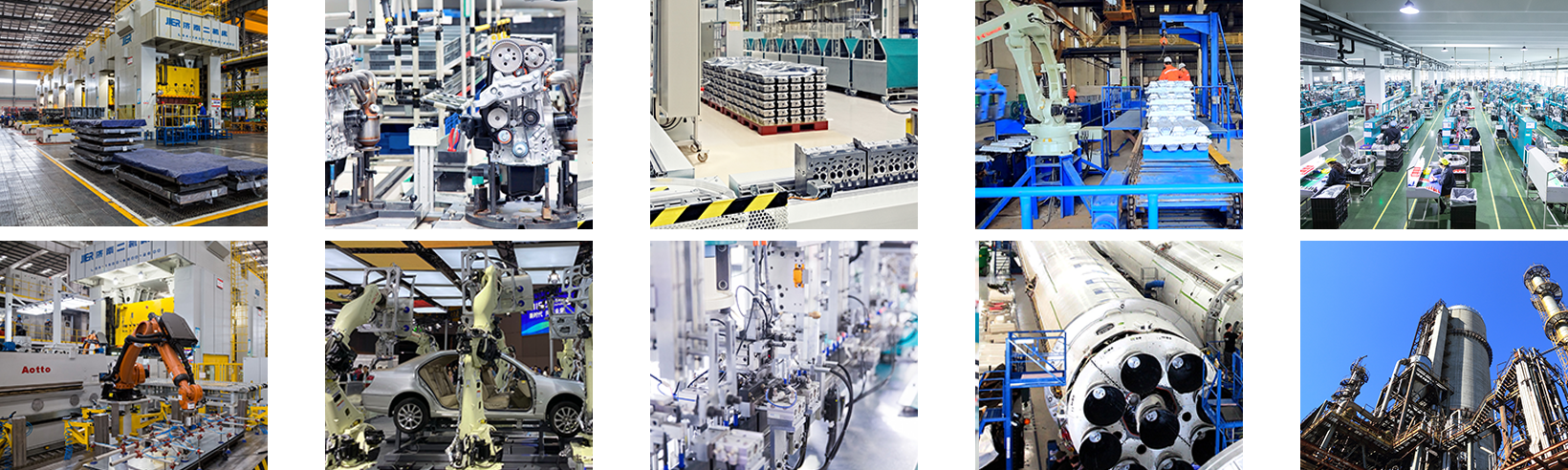