客户痛点
对进口设备依赖度高
汽车制造企业长期依赖进口PLC设备,核心技术受制于人,缺乏自主创新能力,难以灵活应对市场变化和客户需求调整,无法快速优化生产设备。
维护成本高昂
进口设备维护费用高,且维修周期长,容易影响生产进度,进而对产品质量和企业品牌形象造成负面影响。
数据安全风险
依赖进口PLC设备可能存在数据安全隐患,企业关键生产数据和工艺参数面临泄露风险,影响企业核心竞争力。
定制化需求难以满足
进口PLC系统通常为通用型设计,难以满足汽车制造企业对特定生产工艺的定制化需求,限制了生产线的灵活性和效率提升。
系统兼容性差
进口PLC设备与国产化系统兼容性不足,导致企业在技术升级和系统集成时面临困难,增加了实施复杂性和成本。
解决方案
在汽车制造领域,PLC作为工业自动化系统的核心组成部分,推动其国产化进程对于提升国家工业实力至关重要。 华龙讯达全自主大型PLC产品JIC PLC 8010在汽车制造企业大型柔性飞轮智能装配单元上得到成功应用。飞轮智能装配单元国产化PLC改造在不改变原系统的拓扑结构情况下,采用华龙讯达基于龙芯3A5000的全自主PLC控制器(JIC PLC 8010)分别替代西门子S7-1500 PLC(主控PLC,CPU 1513-1 PNT)和S7-1200 PLC(上料PLC,CPU 1214C)。
高精度控制
采用JIC PLC 8010控制器作为主站,通过EtherCAT总线连接I/O从站,实现高速、精准的数据传输和设备控制。
高效协同
在I/O从站加装RPOFINET通讯模块,实现与其他子系统(PROFINET 设备)的通讯连接,确保系统的高效协同运行。
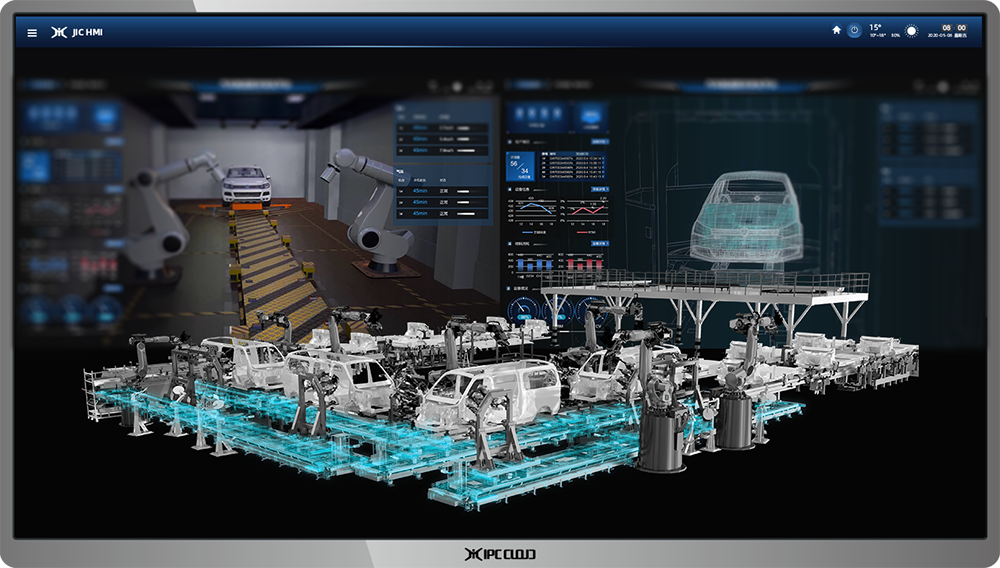
数据实时性和准确性
两套JIC PLC 8010控制器(总控PLC与上料装置PLC)之间的通讯采用基于TCP/IP的网络变量通讯方式进行数据交互,确保信息传递的实时性和准确性。
价值体现
解决进口设备依赖问题
通过国产化替代,华龙讯达PLC帮助企业摆脱对进口设备的依赖,提升了自主创新能力,能够灵活应对市场变化和客户需求调整,快速优化生产设备。
降低维护成本
国产PLC设备维护成本显著低于进口设备,且维修响应速度快,减少了因设备故障导致的生产停滞,保障了生产效率和产品质量。
保障数据安全
基于龙芯3A5000芯片的国产PLC系统从硬件到软件均实现自主可控,有效降低了数据泄露风险,保护了企业关键生产数据和工艺参数的安全。
满足定制化需求
华龙讯达PLC可根据汽车制造企业的特定生产工艺需求进行定制化开发,提升生产线的灵活性和效率,助力企业实现更高水平的自动化生产。
提升系统兼容性
国产PLC设备与国内自动化系统高度兼容,降低了技术升级和系统集成的复杂性,为企业后续技术迭代提供了便利。
成功案例
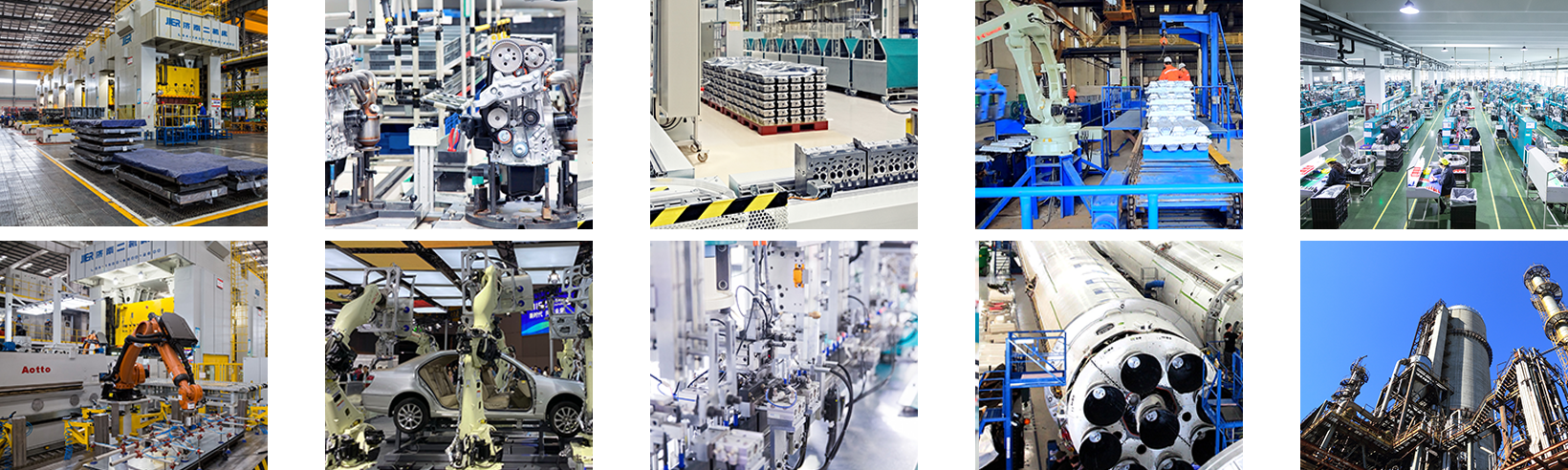